Imagine a future where houses can be built at a fraction of the cost and time it takes today, a future where architectural creativity is not constrained by traditional building methods, and where sustainable living is not just a dream but an attainable reality. This is not a scene from a science fiction movie but a rapidly approaching reality thanks to the advent of 3D printed houses. Over the past few decades, 3D printing technology has evolved from creating small plastic prototypes to constructing full-sized, livable homes. This transformation is poised to revolutionize the construction industry, offering innovative solutions to some of the most pressing challenges we face today, including housing shortages, affordability, and environmental sustainability.
The concept of 3D printed houses might sound futuristic, but it’s already making waves across the globe. The idea is simple yet profound: using large-scale 3D printers to layer materials such as concrete or composite mixes to create the structural elements of a house directly from a digital model. This process eliminates the need for traditional building materials and methods, significantly reducing waste, labor costs, and construction time. With the ability to print homes in a matter of days, this technology is not just about speed; it’s about rethinking how we approach building from the ground up.
The journey of 3D printed houses began in the early 2000s with visionary engineers and architects who saw the potential of applying 3D printing technology to construction. What started as experimental prototypes has now blossomed into a burgeoning industry with real-world applications. Companies around the world are racing to perfect the technology and scale it up to meet the growing demand for affordable and sustainable housing. From the United States to China, the Netherlands to Dubai, 3D printed homes are being built, inhabited, and celebrated for their innovation and efficiency.
One of the most compelling aspects of 3D printed houses is their potential to address the global housing crisis. Traditional construction methods are often slow, expensive, and environmentally taxing. In contrast, 3D printing offers a faster, cheaper, and more sustainable way to build. For instance, in developing countries and areas affected by natural disasters, where housing is urgently needed, 3D printed homes can provide a quick and effective solution. The ability to rapidly deploy housing units in such scenarios can make a significant difference in the lives of many people.
Moreover, the environmental benefits of 3D printed houses are substantial. The construction industry is one of the largest contributors to global waste and carbon emissions. By minimizing material waste and utilizing eco-friendly materials, 3D printing technology can drastically reduce the environmental footprint of building new homes. Some companies are even exploring the use of recycled materials and bioplastics, further enhancing the sustainability of 3D printed homes.
But the advantages don’t stop at speed and sustainability. The design flexibility offered by 3D printing is another game-changer. Traditional construction methods can be restrictive when it comes to architectural design, often limited by the need for specific materials and manual labor. With 3D printing, architects and designers have the freedom to experiment with new shapes, curves, and structures that were previously too complex or expensive to build. This opens up a world of possibilities for creating aesthetically pleasing and functional homes that cater to the diverse needs and tastes of homeowners.
Despite its promising potential, the adoption of 3D printed houses is not without challenges. Regulatory frameworks, building codes, and public perception need to evolve to accommodate this new technology. Initial costs for the equipment and materials can be high, though they are expected to decrease as the technology matures and becomes more widespread. Additionally, while the concept of living in a 3D printed home may still seem unconventional to some, increasing awareness and successful real-world applications are gradually shifting public opinion.
As we stand on the brink of this new era in construction, the possibilities seem endless. 3D printed houses are more than just a technological novelty; they represent a fundamental shift in how we think about building homes. By addressing key issues such as affordability, speed, sustainability, and design flexibility, 3D printed houses have the potential to transform our living spaces and improve the quality of life for countless people around the world. The future of housing is being printed today, layer by layer, bringing us closer to a world where everyone can have access to a safe, affordable, and beautiful place to call home.
I. Understanding 3D Printed Homes
3D printed houses are a groundbreaking innovation in the construction industry, utilizing advanced 3D printing technology to create the structural components of a house layer by layer from digital models. This method fundamentally differs from traditional construction, which typically involves manually assembling materials on-site. In 3D printing, large-scale printers extrude materials such as concrete, plastic, or composites, precisely building up the layers to form walls and other structural elements. This automation not only accelerates the building process but also enhances precision and reduces waste.
The advent of 3D printed houses marks a significant shift in how we approach construction. Imagine a massive 3D printer, much like the ones used for small-scale prototyping but on a much larger scale, meticulously laying down material according to a pre-set design. This technology can construct a basic house structure in a matter of days, compared to the months required for traditional building methods. The result is a sturdy, durable home that meets all safety standards and building codes, but at a fraction of the time and cost.
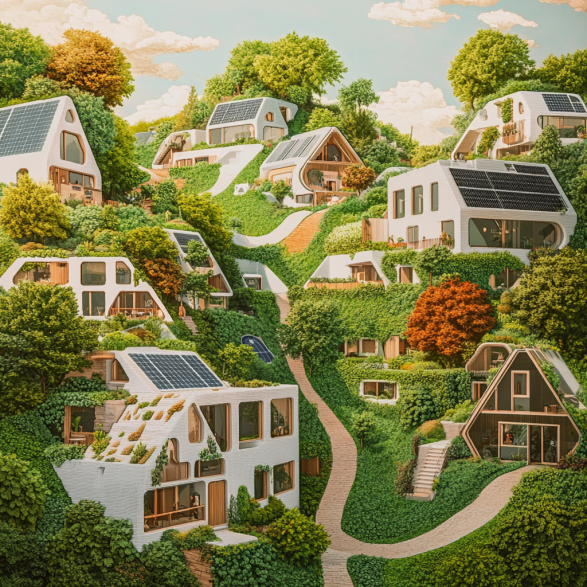
II. The Genesis of 3D Printed Homes
The journey of 3D printed houses began as an ambitious idea, inspired by the potential of additive manufacturing technologies that were initially developed for smaller-scale applications. The concept of using 3D printing for construction can be traced back to the early 2000s, when researchers and innovators began exploring the possibilities of applying this technology to the building industry.
One of the earliest visionaries was Dr. Behrokh Khoshnevis, a professor of engineering at the University of Southern California. In the early 2000s, he developed a process called Contour Crafting, which proposed using large-scale 3D printing to automate the construction of whole structures. His research demonstrated that a robotic system could extrude layers of concrete to build walls and other structural components, significantly reducing construction time and labor costs.
The first practical experiments with 3D printed construction took place around 2008. During this period, various universities and research institutions began developing prototype machines capable of printing small-scale structures. These early prototypes were rudimentary and primarily served as proof-of-concept models, demonstrating that 3D printing could indeed be scaled up to create larger structures. One notable project was the D-Shape printer, developed by Italian architect Enrico Dini. The D-Shape printer used a binder jetting process to create stone-like structures, paving the way for future innovations in 3D printed construction.
The real breakthrough came in the 2010s when technological advancements and increased investment enabled the transition from prototypes to full-scale buildings. In 2014, the Chinese company WinSun made headlines by 3D printing ten small houses in just 24 hours using a proprietary concrete mixture and large-scale printer. This achievement showcased the potential of 3D printing to revolutionize the construction industry by significantly reducing build times and costs.
Following WinSun’s success, several other companies and projects emerged, each pushing the boundaries of what could be achieved with 3D printing technology. In 2015, the first 3D printed office building was completed in Dubai, highlighting the versatility of 3D printing in creating complex architectural designs. This project was a collaboration between WinSun and the Dubai government, further cementing the city’s reputation as a hub for innovation.
As the technology evolved, so did its applications. In 2017, ICON, an American construction technologies company, unveiled a 3D printed house at the South by Southwest (SXSW) festival in Austin, Texas. This house was printed in just 24 hours at a cost of around $10,000, demonstrating the potential for affordable housing solutions. ICON’s approach utilized a proprietary Vulcan printer and a specially formulated concrete mix, designed to be resilient and sustainable.
Other notable projects included the creation of the first 3D printed bridge in Madrid in 2016 and the first 3D printed community in Mexico in 2019, where non-profit organization New Story partnered with ICON to build homes for low-income families. These projects illustrated the expanding possibilities of 3D printing in various construction applications, from infrastructure to humanitarian efforts.
III. Global Leaders in 3D Printed Buildings and Structures
3D printed buildings and structures are cropping up around the world, with several countries emerging as pioneers in adopting this revolutionary technology. These countries are not only exploring the capabilities of 3D printing in construction but also pushing the boundaries of what’s possible. Here’s a look at where 3D printed structures are making an impact and which countries are leading the charge in the use of these printers.
- United States
The United States is at the forefront of 3D printed construction, with numerous innovative projects underway. Companies like ICON and Apis Cor are spearheading efforts to develop affordable housing solutions. ICON, based in Texas, has completed several projects, including the first permitted 3D printed home in the U.S. and a community of 3D printed homes for the homeless in Austin. The U.S. also saw the construction of the first 3D printed office building in California by the company Mighty Buildings.
- China
China is a significant player in the 3D printed construction industry, with numerous large-scale projects. The Chinese company WinSun is a global leader, known for 3D printing ten small houses in just 24 hours and constructing a five-story apartment building and a villa. These projects have showcased China’s capability to leverage 3D printing technology for rapid and cost-effective construction.
- The Netherlands
The Netherlands has been a hub of innovation in 3D printed architecture. In 2016, the first 3D printed bridge was unveiled in Amsterdam, designed for cyclists and pedestrians. The country is also home to the first habitable 3D printed house, part of Project Milestone in Eindhoven, which is an initiative to create a series of 3D printed homes designed to demonstrate the viability and benefits of this construction method.
- Dubai, United Arab Emirates
Dubai has set ambitious goals for integrating 3D printing into its construction sector. The city aims to have 25% of its buildings 3D printed by 2030. One of the most notable achievements is the 3D printed office of the Future, the world’s first fully functional 3D printed office building. Dubai’s government is actively promoting 3D printing technology as part of its strategy to become a hub for innovation.
- Russia
Russia is making strides in 3D printed construction with companies like Apis Cor, which is known for 3D printing a house in just 24 hours during an experiment in the harsh Russian winter. This demonstration highlighted the potential for 3D printing to work in extreme conditions, expanding the possibilities for where this technology can be used.
- Italy:
Known for the D-Shape printer developed by Enrico Dini, Italy has been a pioneer in 3D printing structures, including a large 3D printed house in the Massa Lombarda area.
- Mexico:
In collaboration with ICON, the non-profit organization New Story built the first 3D printed community in Tabasco, Mexico, aimed at providing housing for low-income families.
These countries are not only adopting 3D printing technology but also pushing its boundaries, demonstrating its potential to revolutionize the construction industry. As technology advances and becomes more accessible, we can expect to see even more countries embracing 3D printing for building homes and other structures, paving the way for a future where construction is faster, cheaper, and more sustainable.
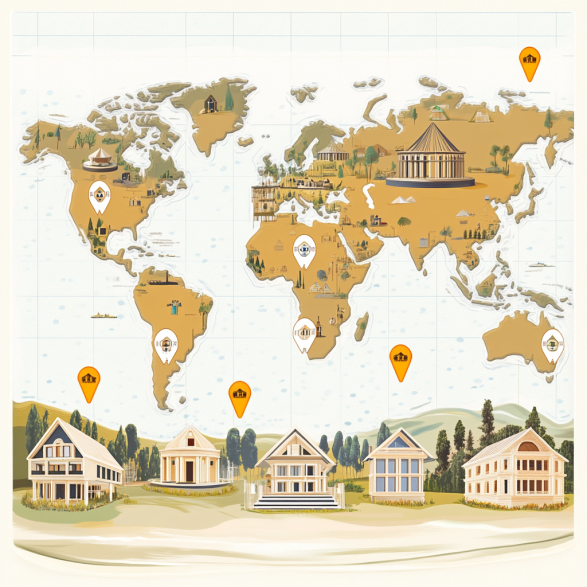
IV. How Much Does It Cost to Make a House with 3D Printing?
The cost of making a house with 3D printing can vary widely depending on several factors, including the size and complexity of the design, the materials used, labor costs, and the specific 3D printing technology employed. However, 3D printing in construction generally promises significant cost savings compared to traditional building methods. Here’s a detailed breakdown of the factors that influence the cost of 3D printed houses and some examples to give you a clearer picture.
Factors Influencing the Cost:
- Size and Design Complexity:
- Larger houses with more complex designs will naturally cost more due to the increased amount of material and time required to print.
- Simpler, smaller structures can be printed more quickly and with less material, reducing overall costs.
- Materials Used:
- The type of material used for 3D printing can greatly affect the cost. Common materials include concrete, composite mixes, and sometimes recycled materials.
- High-performance or eco-friendly materials may increase the cost but offer benefits in terms of sustainability and durability.
- Labor Costs:
- Although 3D printing significantly reduces the need for manual labor, skilled operators are still required to manage the printing process and perform finishing tasks such as installing windows, doors, and utilities.
- Labor costs will vary depending on the location and the complexity of the construction.
- Printing Technology:
- Different 3D printers have different capabilities and costs. High-end printers with advanced features can be more expensive but may offer faster and more precise printing.
- The initial investment in 3D printing equipment can be high, although these costs are expected to decrease as the technology becomes more widespread.
- Location:
- The cost of land and local building regulations can also impact the overall cost. Areas with higher land prices or stricter building codes may see higher costs for 3D printed houses.
Cost Examples:
- ICON’s Vulcan Printer (USA):
- ICON, an American company, has developed the Vulcan printer, which can build a 350 square foot house in about 24 hours at a cost of approximately $10,000. This figure includes the basic structure but not additional finishes or land costs.
- WinSun (China):
- WinSun, a Chinese company, made headlines by 3D printing ten small houses in a single day, each costing about $5,000 to build. These were basic structures, and additional costs for interior finishes and utilities would apply.
- Apis Cor (Russia):
- Apis Cor built a 400 square foot house in Russia for around $10,000. This included the cost of printing the walls but did not cover interior fittings and finishes.
- Project Milestone (Netherlands):
- In Eindhoven, the Project Milestone initiative is creating a series of 3D printed homes. The first house, which is more architecturally complex, had higher costs due to its unique design and compliance with Dutch building standards. The overall cost for these houses varies but is estimated to be competitive with traditional construction methods.
Comparing to Traditional Construction:
- Traditional Construction Costs:
- Building a traditional house can cost anywhere from $100,000 to several hundred thousand dollars, depending on location, size, and materials. Labor costs are a significant portion of this expense.
- Potential Savings:
- 3D printing can reduce construction costs by up to 30-50% primarily due to reduced labor, faster build times, and minimized waste.
Additional Costs:
- Finishing Touches:
- Costs for installing windows, doors, electrical systems, plumbing, and interior finishes are additional and can vary widely.
- Landscaping and other site-specific improvements are also not included in the initial 3D printing cost.
- Permits and Inspections:
- Securing the necessary permits and passing inspections are required costs that vary by region.
V. Benefits of Living in a 3D Printed Home
3D printed houses offer several transformative benefits. The speed of construction is a game-changer, particularly in addressing urgent housing needs in disaster-stricken areas or rapidly growing urban centers. The reduction in labor costs and material waste translates to significant savings, making homes more affordable. Moreover, the design flexibility inherent in 3D printing allows for innovative architectural styles and personalized designs that are often impossible or prohibitively expensive with conventional construction techniques.
Sustainability is another critical advantage. 3D printing uses only the material necessary for the structure, minimizing waste. The technology also opens doors for using recycled materials in construction, further reducing the environmental footprint. For instance, some companies are experimenting with eco-friendly materials such as recycled plastics or bio-concrete, which could make the construction process even greener.
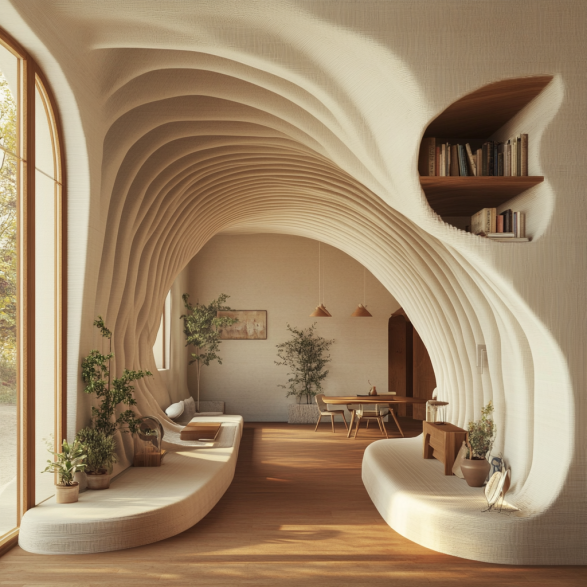
VI. Challenges of printing 3d houses
Additionally, the precision of 3D printing ensures a high level of structural integrity and durability. Each layer is precisely placed according to digital blueprints, reducing the likelihood of human error and resulting in a consistently high-quality build. This precision also allows for the integration of smart technologies and advanced insulation materials within the walls, improving the energy efficiency of the homes.
While the potential of 3D printed houses is vast, several challenges remain. Regulatory hurdles and building codes need to evolve to accommodate this new method of construction. The initial cost of 3D printers and the required materials can be high, although these costs are expected to decrease as the technology becomes more widespread and efficient. Public perception and acceptance of 3D printed homes also need to be addressed, as potential buyers may be hesitant to trust a relatively new and unconventional building method.
Conclusion
The advent of 3D printed houses marks a transformative milestone in the construction industry, promising to reshape how we build and live. With the ability to construct homes rapidly and at a fraction of the cost of traditional methods, 3D printing technology addresses some of the most pressing challenges in housing today. From reducing labor costs to minimizing material waste, the benefits of this innovative approach are significant. It offers a practical solution to the global housing crisis, making affordable and sustainable living a more attainable reality for many.
Beyond affordability, the environmental impact of 3D printed homes cannot be overstated. Traditional construction methods contribute significantly to global waste and carbon emissions. In contrast, 3D printing uses only the necessary materials, reducing waste and often incorporating eco-friendly or recycled substances. This not only lessens the environmental footprint but also promotes a more sustainable approach to building. As the world increasingly prioritizes sustainability, 3D printed homes are poised to play a crucial role in the future of green construction.
The flexibility in design offered by 3D printing technology also revolutionizes architectural possibilities. Architects and designers are no longer limited by conventional construction constraints, allowing for the creation of complex, bespoke structures that are both functional and aesthetically pleasing. This opens up new opportunities for personalized housing solutions that can be tailored to meet individual needs and preferences, further enhancing the appeal of 3D printed homes.
Despite the promising future, the widespread adoption of 3D printed houses faces several hurdles, including regulatory challenges, high initial costs for equipment, and public skepticism. However, as successful projects continue to emerge worldwide and the technology advances, these barriers are likely to diminish. The growing body of evidence supporting the efficiency, cost-effectiveness, and sustainability of 3D printed homes suggests that they will become an integral part of the construction landscape. As we look to the future, 3D printing holds the potential to redefine how we approach building, offering a beacon of hope for affordable and sustainable housing solutions globally.
FAQs
What is a 3D printed house?
A: A 3D printed house is constructed using 3D printing technology, which layers materials such as concrete to build walls and other structural components directly from digital models.
How long does it take to 3D print a house?
A: A basic 3D printed house can be constructed in as little as 24 hours, though more complex designs may take several days to complete.
How much does it cost to build a 3D printed house?
A: The cost of building a 3D printed house can start as low as $10,000 for a basic structure, with additional costs for finishes and utilities.
Can I customize the design of a 3D printed house?
A: Absolutely. One of the main advantages of 3D printing technology is its flexibility, allowing for highly customizable designs tailored to individual preferences.
Are 3D printed houses durable?
A: Yes, 3D printed houses are designed to meet building codes and standards, using materials like concrete that provide strength and durability comparable to traditional construction.
Are 3D printed houses environmentally friendly?
A: Yes, 3D printed houses can be more environmentally friendly due to reduced material waste and the potential use of recycled or eco-friendly materials.
What materials are used in 3D printed construction?
A: Common materials include concrete, composite mixes, and sometimes recycled materials. The choice of material can depend on the design and specific requirements of the building.
Do 3D printed houses meet building regulations?
A: 3D printed houses are built to comply with local building codes and regulations. However, regulatory acceptance can vary by region, so it’s important to check local requirements.
Where can I find 3D printed houses?
A: 3D printed houses are being built worldwide, with notable projects in the United States, China, the Netherlands, Dubai, and Russia.
How do I finance a 3D printed house?
A: Financing options for 3D printed houses are still developing, but as the technology becomes more mainstream, more lenders are offering loans and insurance for these innovative homes.